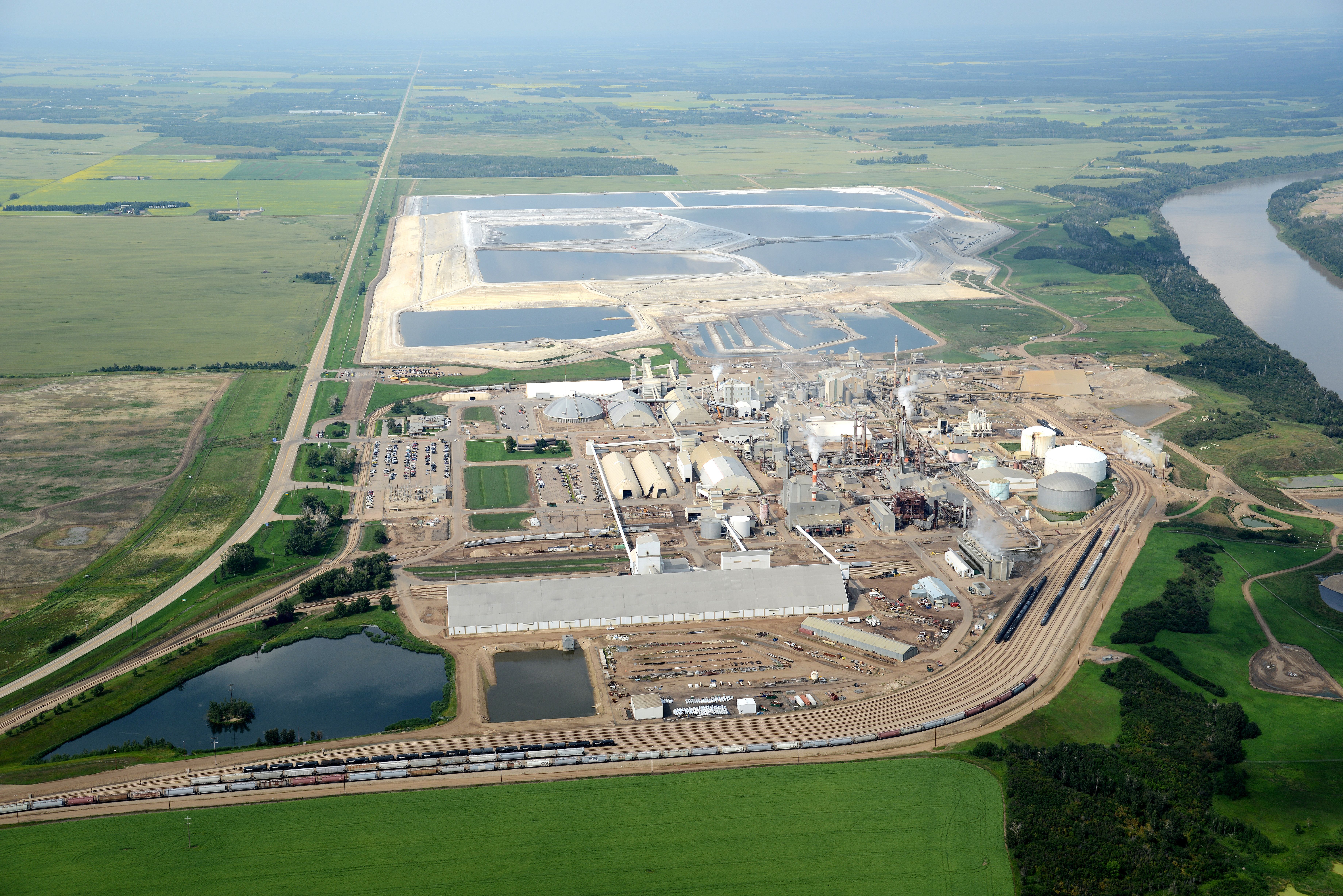
Full steam ahead
Each year, the team at Nutrien’s Nitrogen facility in Redwater, Alberta, Canada loads and ships approximately two million tonnes of nitrogen products. Of that, 60 percent is transported off-site via rail cars. Canadian National Railway (CN) brings empty rail cars to the site, and the Redwater Loadout team, which consists of about 50 people, distributes the cars around our rail yard, loads them with Nutrien’s various product lines and then stages them to be pulled out by CN. With such a high volume of rail movements each day, the focus is on developing innovative solutions to ensure personnel, operational and environmental safety by preventing potential incidents, such as derailments.
Learning lessons
In March of 2023, there was a derailment at the site caused by a run-through switch event. Luckily, the car was empty, so there was not a spill, and no one was nearby, so there were no injuries. While this was a minor incident with no safety, health or environmental impacts, it prompted the team to find and implement solutions rooted in technology.
A switch is what directs rail traffic down its intended path; it moves back and forth to allow a rail car to go in one of two directions. A run-through switch event occurs when a rail car makes a trailing movement through a misaligned switch, which can result in damage to the switch itself and cause a derailment. During the site’s run-through switch event, the lead end of one of the trains was moving in one direction while the rest of the train (on the other side of the switch) went the opposite way, which resulted in a derailment. When investigating the derailment, along with run-through switch events that had occurred in previous years, they realized that the cause was, and typically is, not knowing which way a switch is aligned. The team set out to solve the challenge of preventing people from forgetting in order to avoid future derailments and improve the safety of railroading
Mapping the future
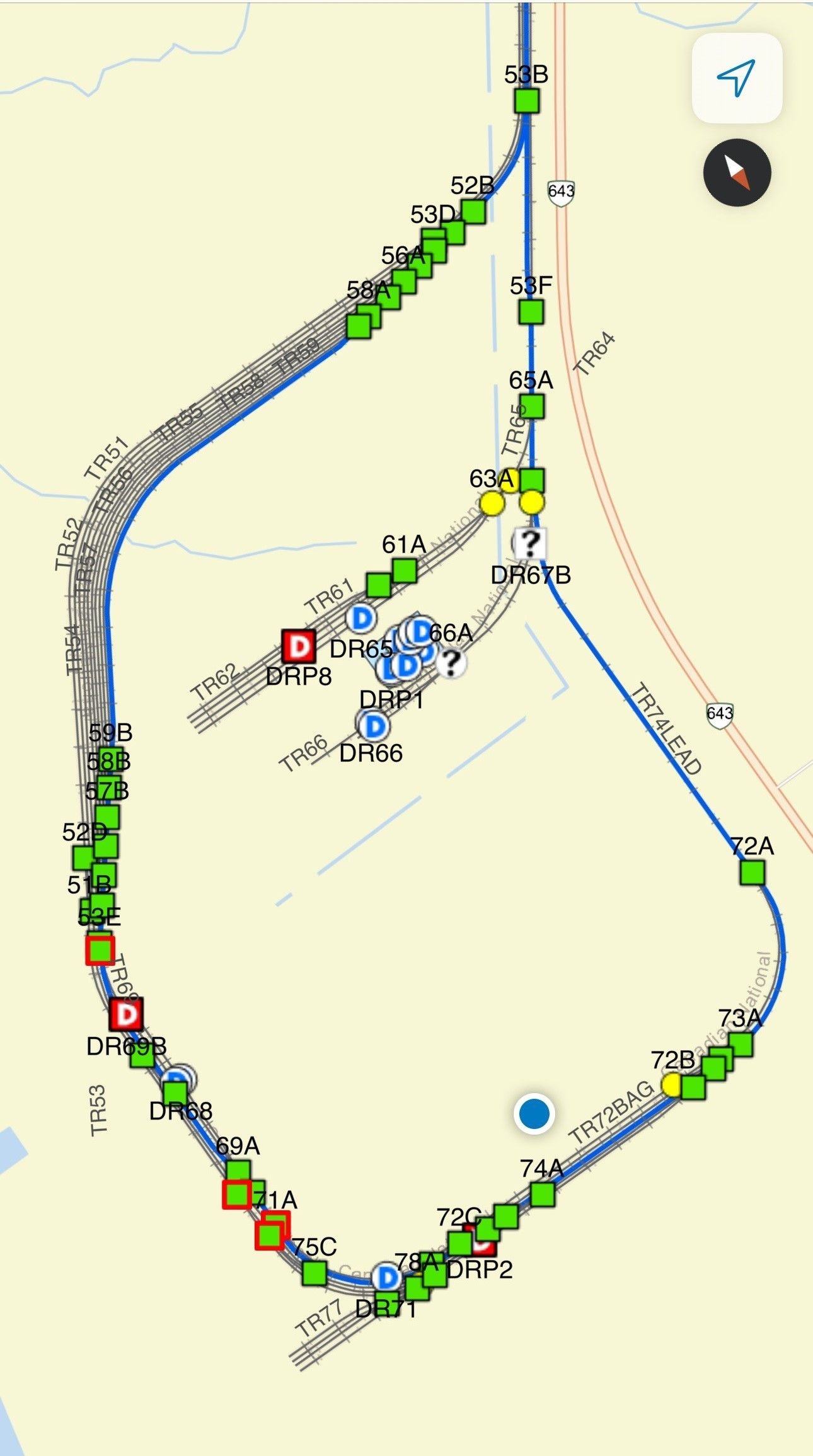
The site’s switch position map includes all switches, fixed and portable derails, and tracks.
The team’s first idea was to create a switch position map. The thought was: we have Google Maps for cars, why not have something like that for railroading? They created a map of the rail yard that includes all the switches and their last known positions. As switches are moved into either normal or reverse positions, the team updates the map accordingly. The map is incredibly useful as both a planning and training tool. Before a track team sets out, they check the map and plan their route based on the switches they’ll interact with, which helps lower the chance of a switch being forgotten. For new employees, the map is useful as a training tool because it provides a visual of the entire yard for them to study. At Redwater, there is a site LTE network that provides cellular coverage across the plant and rail yard. Each track crew has an iPad, so they can easily reference the map on their device anywhere in the yard. Leveraging technology in this way is allowing the team to update and communicate switch positions and rail movements in real time.
The team also uses safety devices called derails to prevent cars from moving or entering areas of the site when they’re not supposed to. For example, derails are set up as additional protection when team members are loading an ammonia rail car or performing maintenance work on a section of track. Some of the devices are fixed in position and can be moved into either an active or de-active state, whereas others are portable and temporary. All the derail devices are also included on the map and kept up to date.
In its current state, the map has many benefits in terms of planning and training, but the team is excited to expand the tool with new infrastructure that layers in automation. They are working to install sensors on the switches that will send signals indicating whether a switch is in the normal or reverse position, and in less than 30 seconds of a switch being thrown, the map will be updated. The team is in the process of installing and beta testing a gateway to receive this information from transmitters and broadcast it to the map. This technology will automatically update the map instead of relying on the team to do it manually.
They are also installing new, solar-powered targets called switch cube targets. Standard switches have targets that are either green, indicating the normal position (straight path), or yellow, indicating the reverse position (diverging track), depending on which way the target is aligned. When a driver is approaching a switch, it can be difficult to see what color it is, especially during the nighttime, dusk or dawn. The switch cube targets not only provide light-up targets that help improve visibility when it’s dark out, they also have arrows that make it more efficient and intuitive to know which path to take.
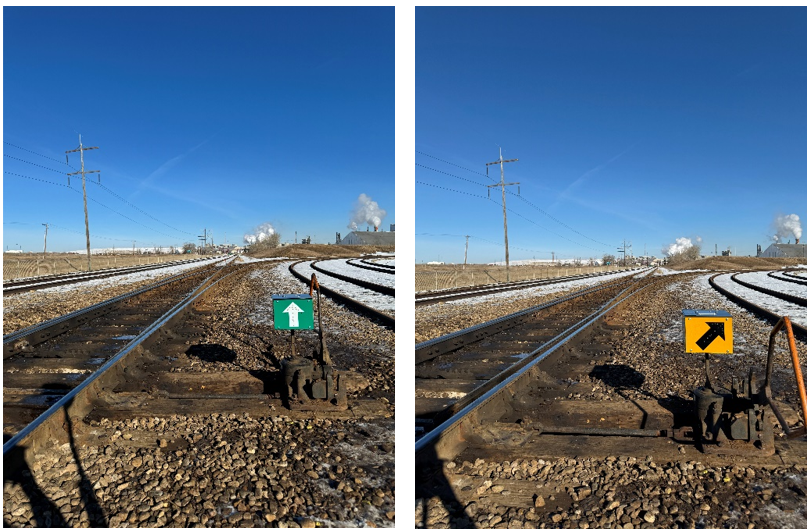
The Switch Cube targets make it easier for train drivers to see which way a switch is aligned as they’re approaching.
The next step will be incorporating geo mapping/geo fencing technology, like positive train control (PTC), so that the locomotive driver will be alerted when approaching a misaligned switch. Nothing like this exists in a rail yard application, so the team at Redwater is looking to introduce similar technology at our site. In a rail yard, trains only move eight miles per hour, so the consequences of a derailment are less severe compared to high-speed trains; however, Nutrien is committed to improving the safety of our people and operations, and this technology will add another layer of safety to railroading.
At various locations, Nutrien has thousands of rail cars in movement every day and 20 Distribution Terminals across North America. As technological advancements are made at Redwater, there will be opportunities to share new tools and equipment, lessons learned and best practices across sites and rail teams to help improve railroading safety.
About Redwater
Redwater, Alberta is located 52 km north of Edmonton. There are currently more than 400 employees working at the facility, and the site has the capacity to produce 951,000 (gross) tonnes of ammonia and other nitrogen-based fertilizers including solid urea, UAN, ammonium nitrate and ammonium sulfate.
Our nitrogen operations at Redwater continue to lead by example, boosting the amount of carbon dioxide (CO2) sequestered through the Alberta Carbon Trunk Line (ACTL) and, by virtue of this, its production of low-carbon ammonia. In 2023, the site completed a CO2 system expansion project to boost CO2 sequestration by an additional 40 percent with the ability to export more than 800 tonnes per year into the ACTL.
Conclusion
The implementation of new technology at Redwater is solidifying Nutrien’s commitment to safety and innovation. By developing solutions such as the switch position map, safety devices and the upcoming automation and geo mapping technology, the team is proactively addressing potential safety hazards and improving operational efficiency. These advancements not only ensure the safety of people and the environment, they also set a precedent for future technological integrations across Nutrien’s sites.
Related stories