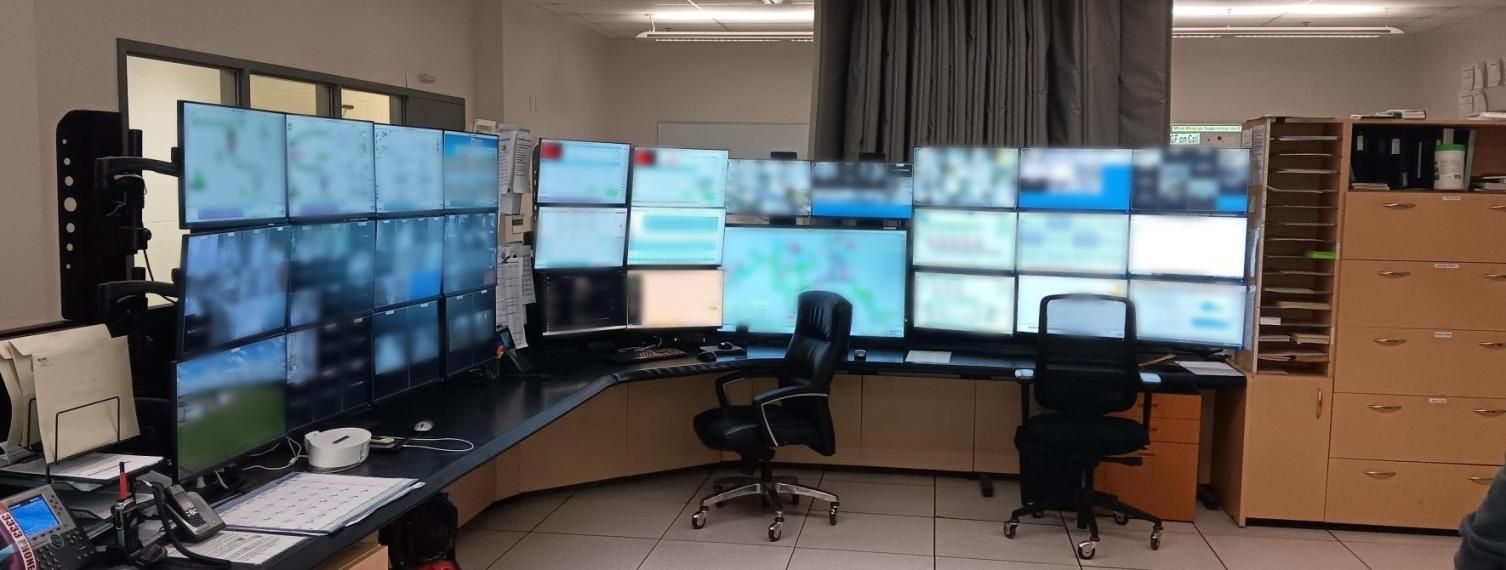
Innovation is Changing the Landscape for Nutrien
When Nutrien opened the first potash mine in Saskatchewan at Patience Lake in 1959, rudimentary tools and machines were the standard as technology wasn’t considered a key factor during those early days, but things have changed a lot.
As Nutrien celebrates 65 Years of Potash Production in the province the technological advancements made over those decades have been staggering as Nutrien is now integrating cutting edge global technology that includes artificial intelligence.
“BeltVision is working, and worth it,” Dylan Stewart, an Employee Driven Reliability Specialist at Rocanville said emphatically.
During his early morning shift on May 10th Dylan experienced firsthand why BeltVision is considered a game changer in the mining industry. That morning, using the artificial intelligence app Dylan noticed that a splice on a conveyor belt had incurred significant damage.
“Under normal conditions, if a splice was noticed in the middle of the night, a decision would be made on whether it is going to last until the belt crew arrives. The panel operator on that shift was surprised to hear from reliability in the late hours of the night. A reliability team member happened to be viewing the active belts that the miners were dumping ore onto that night, as this was happening, the damaged splice was noticed. The damage was significant enough that Operations had to be notified immediately to avoid a failure. The crew captain made the decision to stop the belt and allow our employees to make the repair,” Dylan explained.
Although the belt was damaged, the incident turned out to be a positive.
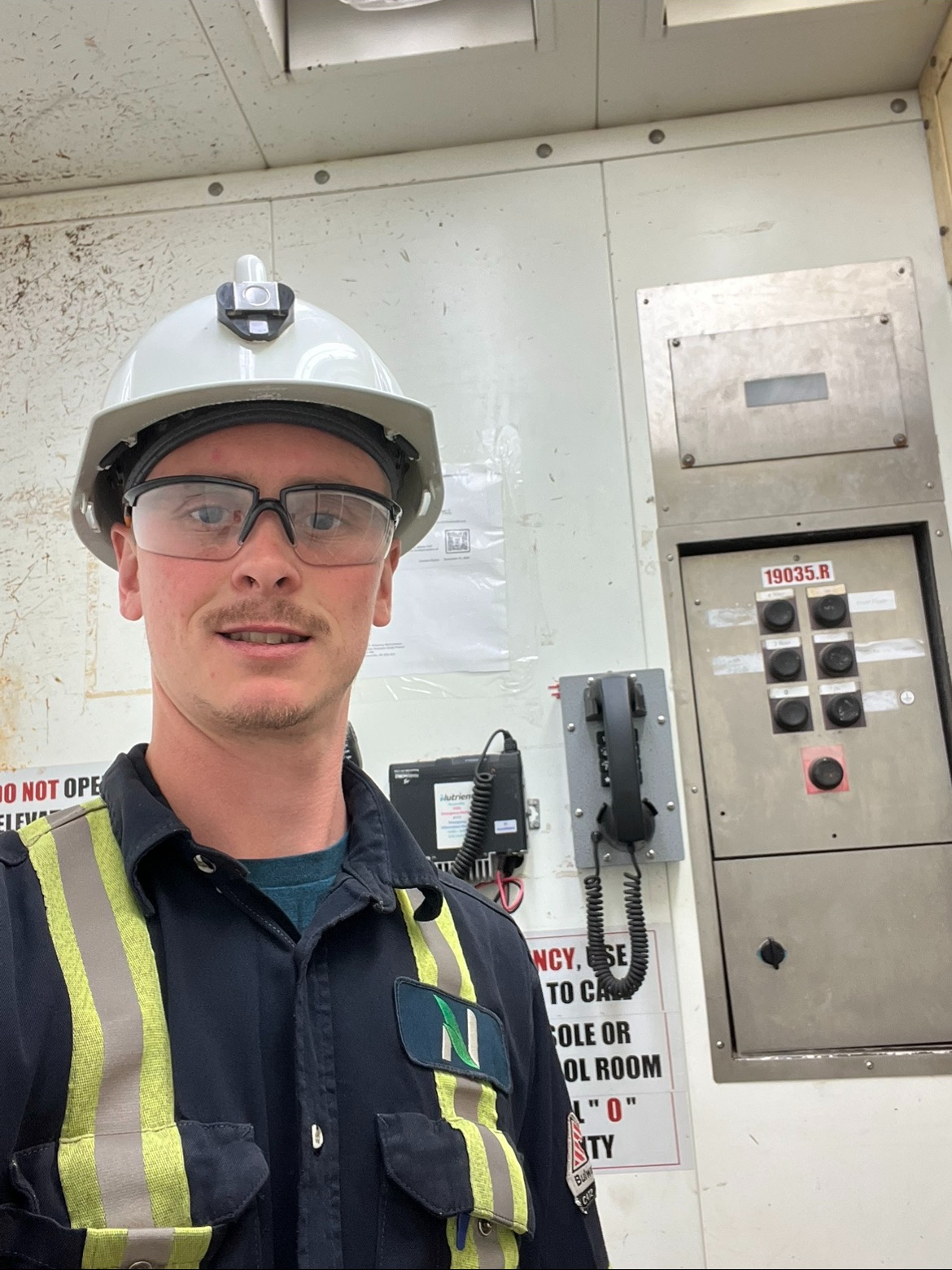
“This opened a lot of positive conversations around proactive maintenance, BeltVision technology, and using operations to repair belts other than miner extensible belts. There were some production employees who were unaware of our ability to monitor splice conditions, this also created positive conversation around communication. Without having the ability to view the splices in detail, we stood a greater chance of having a failure on a splice,” Dylan said.
BeltVision is an application that was first implemented into the Rocanville site in 2020. It was introduced after our Potash team identified the mainline conveyor belts as a significant bottleneck and source of downtime. These belts which are kilometers in length bring the ore from our borers to the hoists that bring it to the surface – they’re the arteries of our sites. One significant recurring potential issue with these belts is splice failures. Mechanical splices – a series of clips that look like a zipper – connect two pieces of belt material, and sometimes they fail.
BeltVision utilizes AI to recognize and analyze belt splices and damage.
“We can see detailed images of splice clips while the belt conveys ore. We also have employees doing a physical visual inspection of the belt and documenting how many damaged splices they observed. We use BeltVision to help determine when we should schedule a repair,” Dylan said.
The success of BeltVision is the result of many teams collaborating to make it happen. Multiple IT teams, such as Digital Transformation, Converged Technology, Connected Worker as well as ETC teams such as Operational Excellence, and our Maintenance and Reliability group were part of the implementation.
Site engineering, site IT, operations and many others also have been a part of making this technology successful and the lessons learned in the implementation extend throughout the Nutrien network.
“The cameras operate in hot, dusty environments. They see a lot of vibration. We must stay on top of keeping the camera lens' clean, and ensuring the proper hardware is installed to keep the camera protected. Several departments play a role in installing a camera and using it for its designed purpose, we are improving communication amongst all involved departments which plays a significant role in why it is working well,” Dylan explains.
Prior to BeltVision being installed, production was regularly halted due to scheduled shutdowns. Manual splice inspections needed to be performed, these inspections were expensive and resulted in downtime.
“These types of catches make a considerable impact when it comes to the value for up time to Nutrien / Potash / Rocanville and help eliminate serious safety risks,” Justin Stade, Director, Commercial Planning & Business Process Improvement stated.
In the last four years the technology has been trialed at other sites, enabling the knowledge transfers within the Nutrien network. BeltVision is just part Nutrien’s commitment to our core values that include safety and integrity as we continue the push to Feed the Future.
“The BeltVision application only works if we have excellent people in charge of reliability like Dylan. He is always up to date on the status of the belts on BeltVision, communicates in a very clear and timely manner with our team at corporate, and is obviously organized and communicative with his team on site (based on how quickly things are fixed, cameras are cleaned, etc.). The benefits of the application are realized because of Dylan’s commitment to safety, integrity, and reliability,” Jayme Mitchell, Data Scientist added.
Related stories