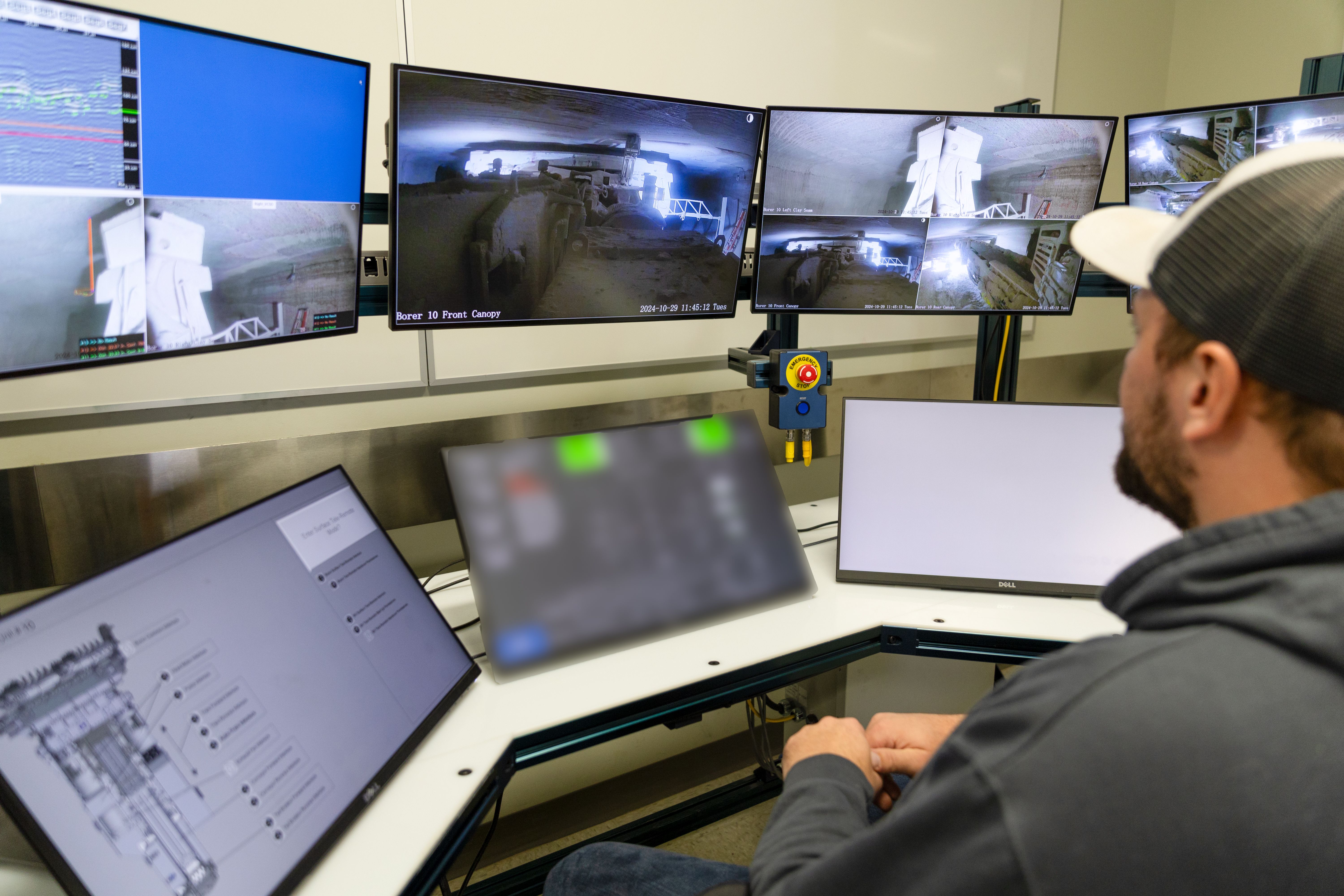
Transforming Mining with Automation: A Journey of Safety and Efficiency
In the ever-evolving world of mining, the integration of advanced automation technologies has paved the way for remarkable improvements in safety and operational efficiency. During our transformative journey of mining automation across our network of mines in Saskatchewan, we have reached a significant milestone of 25 million ore tonnes mined using automation.
“Reaching 25 million ore tonnes cut through our automation program is an outstanding achievement,” says Shannon Rhynold, Vice President, Engineering, Technology and Capital & Operations Strategy, Potash. “We are now on a journey of significant growth, having doubled our tele-remote ore produced each of the last three years. We are on pace to achieve this goal again in 2024 and aim for 40-50% automated ore mined by the end of 2026.”
Lanigan: The Starting Point
Our tele-remote (TR) journey began at Lanigan in 2017, where a simple camera was mounted on a 2-rotor mining machine. This early phase was marked by excitement, followed by a steep learning curve which drove the collaborative spirit of the teams involved.
“This project has truly been a collaborative effort. Early on, our technical team greatly benefited from the expertise and insights of our operators. Their feedback was foundational, and it ultimately shaped the development of the tele-remote system,” says Owen Gunther, Automation Project Lead, Lanigan. “We also relied on our skilled tradespeople, whose practical experience proved vital in adapting the technology to the mining machines for long-term sustainability.”
Cory's Replication Efforts
Our Cory potash mine began its tele-remote replication journey in 2020, following extensive collaboration with the Lanigan team. During this period, Cory focused on upgrading existing mining machines with TR technologies while building new TR-enabled miners to expand our fleet. These ongoing initiatives aim to operationalize the technology to support production needs, ensuring the safe and efficient production of potash.
“Collaboration within the tele-remote project is essential for achieving our shared goals and maximizing the impact of our work. By leveraging the diverse expertise and perspectives within our network, we can tackle complex challenges more effectively and drive innovation,” says Tyler Zimmerman, Automation Project Lead, Cory. “Open communication, mutual respect, and a commitment to collective problem-solving are the cornerstones of our approach, ensuring that every voice is heard, and every contribution is valued. Together, we are not just working on a project; we are building a dynamic, synergistic environment that propels us toward success."
After the successful implementation at Lanigan, Cory replicated the technology, further refining and expanding its application. This replication set the stage for broader adoption across other sites.

Scaling to Other Sites: Vanscoy and Allan
Taking lessons learned from Lanigan and Cory, Vanscoy and Allan embarked on their own journeys to replicate tele-remote technology. This phase involved intricate application processes and adaptation to site-specific conditions.
"Over the past few years, Vanscoy has been able to leverage the lessons learned from other sites, including the development of new technologies and improvements on existing tele-remote technology," says Brian Holonics, Automation Project Lead, Vanscoy. "The sharing of successes between sites has helped Vanscoy expedite replicating their fleet and build additional confidence in operationalizing the equipment. We have clearly seen the benefits of utilizing the technology, including improved safety, additional tonnes, and improved performance on both the borer and continuous haulage system."
"Allan has benefited greatly from the development work that Lanigan and Cory did on the tele-remote system. We were able to quickly begin replicating the system to our mining fleet with only minimal modifications to meet site-specific requirements,” says Mike Siourounis, Continuous Improvement Lead, Allan. “The strong collaboration across the network, including temporary transfers of Allan employees to the Lanigan Automation team, was a significant benefit. The collaboration between the sites continues to provide value as we find further improvements to the automation systems and how our workforce uses them."
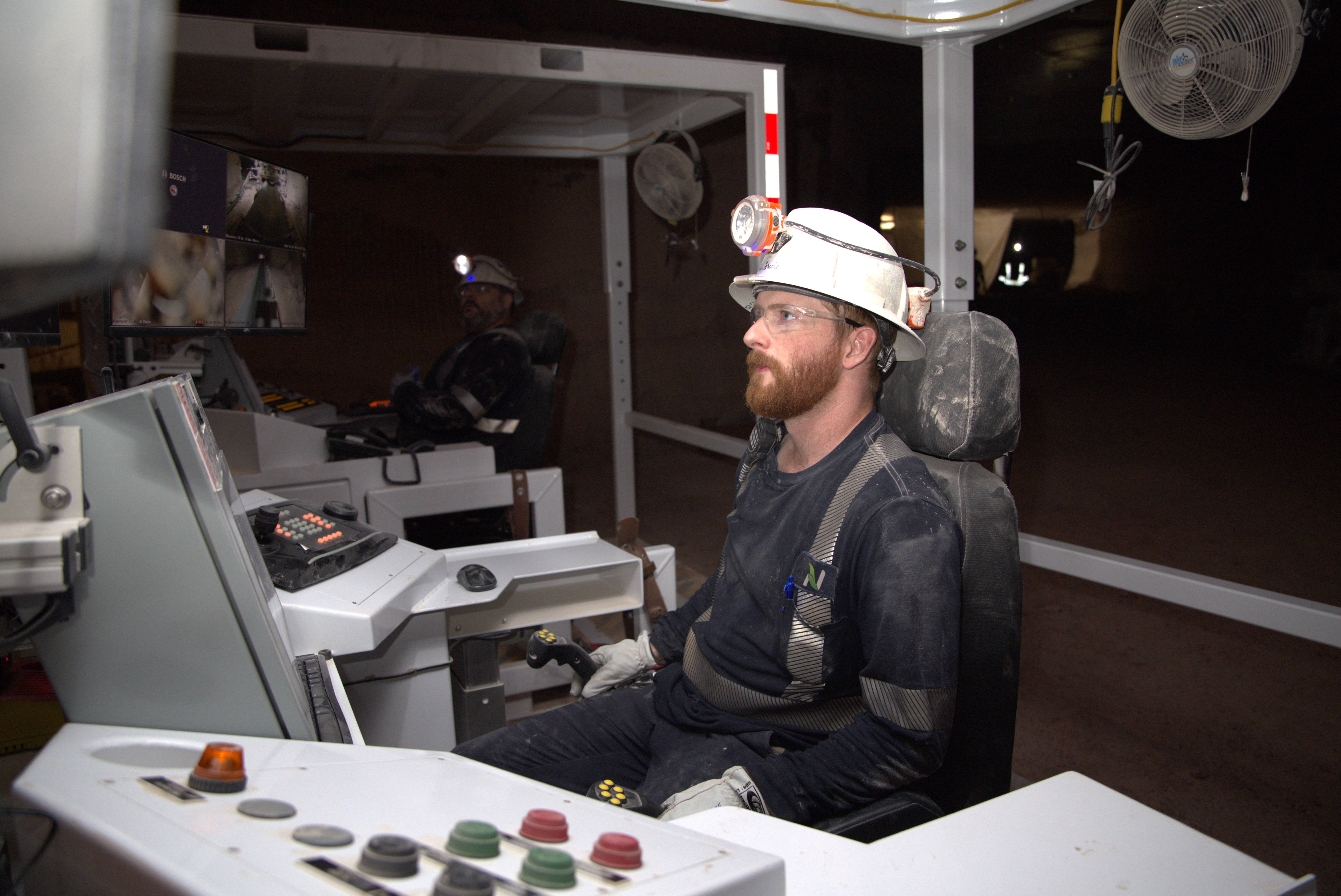
Development at Rocanville
At our Rocanville site, the focus has been on advancing from side pass Operator Not Present (ONP) technology to fully automating the first pass cutting process. This journey, which began in 2018, aimed to revitalize automation technology that had seen little advancement since the early 90s.
"We embarked on revitalizing our side pass technology before moving on to the challenge of automating the manual aspects of our first pass cutting process," says Clayton Lawless, Automation Lead, Rocanville. "Our efforts have led to significant progress, including the deployment of our prototype Belt Builder and advanced steering systems. These achievements are a collaborative effort between our operations and maintenance teams, aimed at improving flexibility, efficiency, and safety."
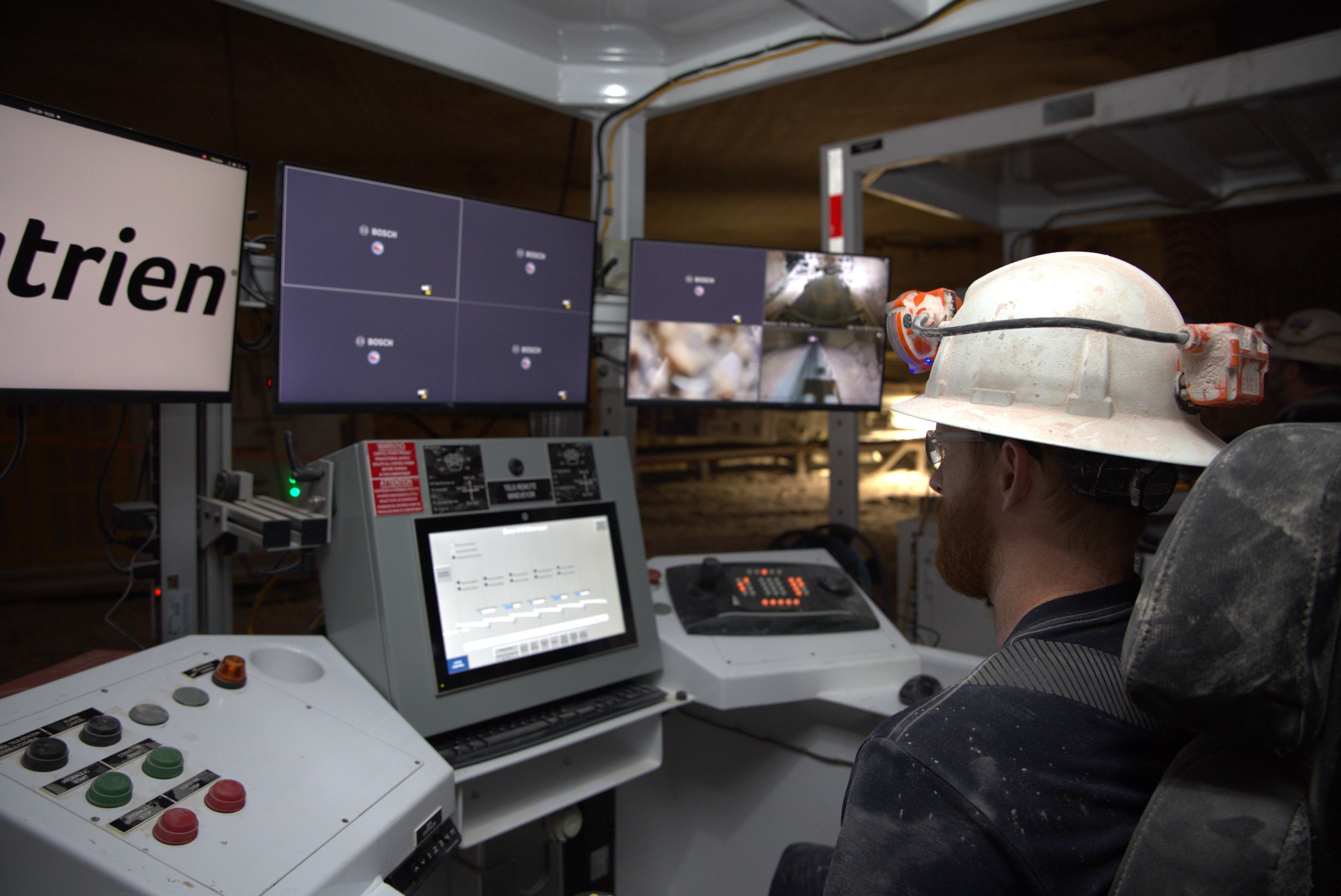
Safety and Efficiency: A Dual Focus
The primary objective of our automation efforts has always been to enhance safety within our mining operations. By reducing the exposure of operators to hazardous conditions, our automation technology significantly improves workplace safety. Additionally, these systems bring substantial productivity benefits, such as eliminating downtime during shift changes and enabling safer mining in areas with challenging geology.
We have ambitious plans to further advance tele-remote, Operator Not Present (ONP), and other cutting-edge automation technologies. These future advancements are designed to transform the industry and set new benchmarks for operational excellence.
"I am incredibly proud of our teams for their dedication and hard work in reaching this milestone of 25 million ore tonnes cut using automation," says Trevor Berg, Senior Vice-President, Potash Operations. "By embracing advanced technologies and fostering a culture of collaboration and innovation, we are not only enhancing the safety and well-being of our employees, but also setting new standards for efficiency in the mining industry. Our journey doesn't stop here; We will continue to push the boundaries of what's possible by listening to the challenges our employees face and then focusing on thoughtful technological applications that solve those problems from a safety and efficiency perspective.”
Related stories